Electrical thermography is the term used when thermal imaging cameras are being used in the electrical industry.
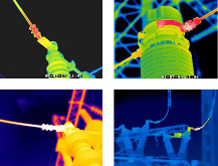
Learn about Thermal Imaging use for Electrical Applications
Electrical thermography is the term used when thermal imaging cameras are being used in the electrical industry.
Today, electrical equipment is in the centre of manufacturing and plays an important role in every business operation. If the electrical equipment is not working correctly this can hold up businesses such as manufacturers or power plants. Faulty electrical equipment has been known to also cause fires which can severely damage buildings and endanger people's lives.
Thermal Cameras can be used to prevent any sudden halts to power supply or electrical machinery. Thermal Cameras can be used to carry out regular thermal surveys as part of electrical equipment maintenance. Thermal or Infrared (IR) Cameras work by converting emitted radiation levels into a two-dimensional picture that will highlight contrasting energy levels, usually electrical faults will display a rise in temperature which serves as the basis for identifying most electrical faults. Thermal Camera have a lot of advantages for detection of electrical faults as is quick and non-contact which means the equipment can be uninterrupted while the thermal survey is taking place. The thermal images will give a clear picture of current condition of the equipment and the temperature distribution. When the power equipment is in operation, the state of the heat distribution can be seen in the thermal images, this will allow the user to see if the heat distribution is normal or not.
Ideally the person carrying out the thermal survey on the electrical equipment will have some knowledge of infrared or physics and will have received some training on the camera operation in other to evaluate the thermal image that has been produced by the thermal camera.
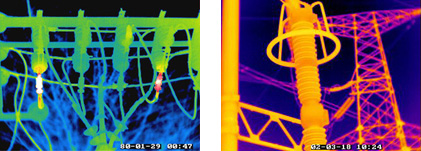
What types of electrical equipment can Infrared Cameras survey?
Infrared Thermal cameras are usually applied to the following monitoring and fault diagnosis of power equipment
- High voltage electrical equipment can be surveyed for faults inside and outside when in operation.
- Various conducting joint, clamp, connection and bad connection can be surveyed for oxidation corrosion defects.
- Various high-voltage switch contacts can be surveyed for exposed flaws that occur within the centre.
- Isolating Switch blade can be surveyed as the combination of contact pad and the rotating ball cap can cause bad defects.
- Overheating capacitor, coupling capacitor and the short of petroleum oil poor insulation (low oil level) defects can be shown with the use of a thermal camera survey.
- Various types of arrester moisture within the centre of defects, the aging of components within the centre or non-linear characteristics of mutation and the defect can be found with a thermal image survey.
- Generator State Test, brush and collector ring contact state detection, overheat detection within the centre can all be detected with a thermal imaging survey.
- Box abnormal overheating of power transformers, eddy current overheating, high and low pressure casing upper and lower ends of a bad connection can all be detected with a thermal imaging survey.
- Various types of motor bearing bad contact, and inside and outside the centre of abnormal overheating can all be detected with a thermal imaging survey.
- Electrical Testing Equipments
- High Voltage AC /DC Testing Kits (HIPOT KITS)
- Ultra Light High Voltage DC Test Sets
- High Voltage AC/DC Dividers
- Primary & Secondary Current Injection Testing Sets
- Vacuum Circuit Breaker Bottle Test Sets
- DC Earth Fault Locator
- Partial Discharge Test Systems
- Transformer Testing
- Circuit Breaker Testing
- Miscellaneous Testing Equipment
- Electrical Safety Equipments
- Condition Monitoring
- Cameras and Imaging Systems